聚晶金剛石的超聲振動(dòng)研磨機(jī)理研究
日期:2009-07-13 | 來(lái)源:機(jī)械專(zhuān)家網(wǎng)
1 引言
聚晶金剛石(PCD)具有接近天然金剛石的硬度、耐磨性以及與硬質(zhì)合金相當(dāng)?shù)目箾_擊性能,PCD刀具的應(yīng)用范圍已逐漸擴(kuò)展到有色金屬和非金屬材料的精加工領(lǐng)域,尤其適用于鋁合金材料的精密..
1 引言
2 超聲振動(dòng)研磨試驗(yàn)及結(jié)果分析
- 試驗(yàn)條件
- 試驗(yàn)結(jié)果分析
- 試驗(yàn)設(shè)備與材料
- 超聲振動(dòng)研磨試驗(yàn)在經(jīng)過(guò)改裝的轉(zhuǎn)速可調(diào)的高精度靜壓式研磨機(jī)上進(jìn)行;研磨盤(pán)采用直徑D=300mm 的高磷鑄鐵盤(pán);磨料為W7 粒度的金剛石研磨粉;試件材料為鄭州新亞復(fù)合超硬材料有限公司生產(chǎn)的JFER1308DF-IV(規(guī)格為Ø13.44×0.8mm,粒度W40)和美國(guó)GE 公司生產(chǎn)的PC1308DA(規(guī)格為Ø13×0.8mm,粒度W20);超聲振動(dòng)研磨系統(tǒng)由J923025型電子管式超聲波發(fā)生器(最大額定輸出功率為250W)、自行研制的磁致伸縮超聲換能器及相應(yīng)的夾具組成;由于研磨加工要求的材料去除量極微小,且PCD材料具有高耐磨性,因此采用ES120G-4型電子天平(稱(chēng)量可精確到10-4g)來(lái)測(cè)量PCD試件的質(zhì)量變化,并以此評(píng)價(jià)研磨加工效率。
- 試驗(yàn)方法與參數(shù)
- 研磨時(shí),試件沿研磨盤(pán)徑向水平方向(垂直于研磨盤(pán)線速度方向)作高頻振動(dòng),工作頻率為19KHz,靜載荷為15N,研磨時(shí)間為60min。試驗(yàn)時(shí),研磨盤(pán)選取三種不同轉(zhuǎn)速(80r/min、320r/min 和500r/min),超聲波發(fā)生器輸出不同功率,分別研磨不同粒度的PCD試樣,并分別測(cè)量試驗(yàn)結(jié)果。
- 超聲振動(dòng)研磨試驗(yàn)結(jié)果如圖1和圖2所示。由圖1可知,超聲振動(dòng)研磨工藝可明顯提高研磨PCD的材料去除率。試驗(yàn)數(shù)據(jù)還顯示,隨著超聲波發(fā)生器輸出功率的增大,PCD材料去除率有較大幅度的提高(超聲波發(fā)生器輸出功率為250W時(shí),PCD材料去除率比普通研磨提高一倍以上),即采用超聲振動(dòng)研磨比普通研磨可獲得更高的加工效率。這是因?yàn)槌暡òl(fā)生器輸出功率的提高使PCD試件的振幅增大,說(shuō)明在超聲振動(dòng)研磨中振幅對(duì)PCD材料去除率的影響很大;由圖1還可看出,在相同試驗(yàn)條件下,隨著研磨盤(pán)轉(zhuǎn)速的提高,PCD材料去除率也相應(yīng)提高。
- 由圖2可知,在相同試驗(yàn)條件下,超聲振動(dòng)研磨粗粒度PCD時(shí)的材料去除率比研磨細(xì)粒度PCD的材料去除率更高,這說(shuō)明合成PCD的金剛石晶粒粒度對(duì)PCD材料的耐磨性和強(qiáng)度有很大影響。
![]() 圖1 超聲波發(fā)生器輸出功率變化時(shí)的PCD材料去除率 |
![]() 圖2 超聲振動(dòng)研磨不同粒度PCD時(shí)的材料去除率 |
3 超聲振動(dòng)研磨PCD的去除機(jī)理分析
- 研磨PCD材料的去除機(jī)理
- 超聲振動(dòng)研磨PCD材料的去除機(jī)理
- 研磨PCD材料的去除機(jī)理主要包括機(jī)械作用和熱化學(xué)作用。在研磨初期,由于PCD的表面粗糙度較大,金剛石晶粒凸出PCD表面較多,使高速運(yùn)動(dòng)的磨粒很容易著力,促使金剛石晶粒容易在底部間接粘結(jié)部分產(chǎn)生應(yīng)力集中。PCD晶粒間的結(jié)合部位是其薄弱環(huán)節(jié),其結(jié)合能小于組成PCD的金剛石單晶體最易解理的(1 1 1)晶面的結(jié)合能。當(dāng)受到磨粒高速撞擊時(shí),由于應(yīng)力逐步集中,使微裂紋沿金剛石晶粒間的結(jié)合部位擴(kuò)展,在磨粒的反復(fù)高速?zèng)_擊下,將發(fā)生沿晶疲勞斷裂,使金剛石微粒發(fā)生整體松動(dòng)并脫落(如圖4 所示)。隨著研磨的繼續(xù)進(jìn)行,PCD表面粗糙度逐步下降,發(fā)生金剛石晶粒整體脫落的情況也逐漸減少。
- 根據(jù)Griffith斷裂力學(xué)理論,某些固體的共價(jià)鍵和離子鍵強(qiáng)度很高,其缺陷相對(duì)來(lái)說(shuō)受到束縛,因而容易在較低應(yīng)力下發(fā)生斷裂(相對(duì)其強(qiáng)度而言),此類(lèi)固體稱(chēng)為脆性固體。如果斷裂的阻力主要取決于固體的固有鍵強(qiáng)度,則該固體可稱(chēng)為高脆性固體。由于PCD材料中金剛石晶粒所占比例高達(dá)80%~90%,去除阻力主要取決于構(gòu)成PCD的金剛石晶粒本身的強(qiáng)度,因此可將PCD材料劃歸為高脆性固體。PCD屬于高脆性多晶固體材料,各個(gè)金剛石晶粒的晶向不同,當(dāng)裂紋遇到兩個(gè)晶粒的邊界時(shí),或者穿過(guò)它在第二個(gè)晶粒中繼續(xù)擴(kuò)展(對(duì)于小角度晶界及高強(qiáng)度晶界,易發(fā)生穿晶斷裂),或者裂紋沿晶界擴(kuò)展。由于金剛石微粒的(1 1 1)晶面裸露的機(jī)率最大,相對(duì)于高速運(yùn)動(dòng)的磨粒較容易著力,高速運(yùn)動(dòng)的磨粒產(chǎn)生與(1 1 1)晶面垂直的拉應(yīng)力,當(dāng)該拉應(yīng)力超過(guò)其臨界值時(shí),即產(chǎn)生裂紋,裂紋沿(1 1 1)晶面方向產(chǎn)生穿晶裂紋,在PCD表面產(chǎn)生光滑的解理斷裂平面和解理臺(tái)階(如圖5所示)。金剛石晶粒的解理性脆斷是在拉應(yīng)力作用下裂紋擴(kuò)展的結(jié)果。由于受孿晶帶的影響以及金剛石的隨機(jī)排列方式,金剛石顆粒的斷裂表面往往呈“之”字形,即在解理面上形成微小的解理臺(tái)階。這是由于許多孿晶帶相互交叉,使裂紋擴(kuò)展方向不得不發(fā)生改變,因此阻礙了裂紋貫穿整個(gè)金剛石。金剛石晶粒的解理性脆斷是研磨PCD的主要去除方式之一。
圖3 PCD的微觀形貌
圖4 晶粒整體剝落后留下的空穴
圖5 PCD解理性脆斷形貌
圖6 PCD表面微觀損傷性劃痕 - 在研磨過(guò)程中,鋒利的磨粒以很高的速度和適當(dāng)?shù)膲毫澾^(guò)PCD,在金剛石晶粒表面產(chǎn)生大量損傷性劃痕(如圖6所示),這些劃痕可分為塑性劃痕和脆性劃痕,這種機(jī)械去除方式也是研磨PCD的一種主要材料去除方式。此外,在PCD的研磨過(guò)程中還存在石磨化去除、熱蝕去除、擴(kuò)散去除、氧化去除等多種熱化學(xué)去除方式,但熱化學(xué)去除方式在PCD材料去除中不占主要地位。
- 在超聲振動(dòng)研磨中,由超聲換能器及相應(yīng)夾具組成的超聲振動(dòng)系統(tǒng)對(duì)PCD材料施加一個(gè)振幅為A(通常A=10~20µm)、頻率為f(通常f=20KHz)的高頻振動(dòng),使PCD材料沿研磨盤(pán)徑向產(chǎn)生一個(gè)振幅為A 的高頻往復(fù)運(yùn)動(dòng),研磨時(shí),這一往復(fù)運(yùn)動(dòng)與研磨盤(pán)線速度V合成,研磨軌跡由普通研磨時(shí)的圓變?yōu)樵趫A上疊加的以f/V為頻率、以A為振幅的高頻諧波,從而使磨粒在單位時(shí)間內(nèi)通過(guò)PCD材料表面的研磨軌跡加長(zhǎng),研磨效率相應(yīng)提高;同時(shí),單位時(shí)間內(nèi)研磨軌跡的加長(zhǎng)也使研磨速度增大,使磨粒具有比普通研磨條件下更高的沖擊動(dòng)能,由此提高了研磨PCD的材料去除率。對(duì)于材料破壞而言,能量的大小固然是一重要因素,而能量對(duì)時(shí)間的作用梯度在某種意義上更為重要。將超聲振動(dòng)引入PCD研磨中,就是通過(guò)超聲波的能量激波作用提高能量梯度和能量聚集,使磨粒在短時(shí)間內(nèi)克服晶間結(jié)合能,使晶粒發(fā)生疲勞破壞(特別是解理性脆斷和微觀損傷性去除)的機(jī)率增大。有學(xué)者指出:金剛石在沖擊載荷的循環(huán)作用下,產(chǎn)生裂紋的應(yīng)力值大大低于所需的靜應(yīng)力。在超聲振動(dòng)研磨中,PCD中的金剛石晶粒始終處于高頻交變沖擊載荷的作用下,加速了PCD材料的疲勞破壞,特別是金剛石晶粒的解理性脆斷。
- 由超聲振動(dòng)研磨軌跡的特點(diǎn)可知,研磨速度方向是在一定夾角內(nèi)(最大可達(dá)60°)以超聲振動(dòng)頻率f高頻擺動(dòng),因此可在金剛石晶粒表面看到大量交錯(cuò)的損傷性劃痕(見(jiàn)圖6),不斷變化的研磨速度方向使金剛石晶粒的易加工晶向經(jīng)常處于研磨速度方向,使金剛石較易去除,從而提高了PCD的材料去除率。
- 從宏觀能量的角度分析,研磨過(guò)程實(shí)質(zhì)上是一個(gè)能量消耗過(guò)程。普通研磨時(shí)能量的輸入全部來(lái)自帶動(dòng)研磨盤(pán)轉(zhuǎn)動(dòng)的電機(jī);而在超聲振動(dòng)加工中,系統(tǒng)的能量輸入不僅來(lái)自帶動(dòng)研磨盤(pán)轉(zhuǎn)動(dòng)的電機(jī),同時(shí)還來(lái)自超聲波發(fā)生器。因此,在其它加工條件相同的情況下,超聲振動(dòng)研磨系統(tǒng)在單位時(shí)間內(nèi)對(duì)研磨區(qū)的輸入功率比普通研磨時(shí)更多,即輸入功率增大;而且由于超聲振動(dòng)研磨的摩擦系數(shù)較普通研磨有減小的趨勢(shì),消耗在摩擦熱上的能量并未因振動(dòng)的引入而發(fā)生較大變化。由于超聲振動(dòng)研磨中的能量聚集和應(yīng)力波作用,使系統(tǒng)消耗在裂紋擴(kuò)展和新表面形成上的能量增加,從而使超聲振動(dòng)研磨的材料去除率增大。
- 此外,超聲振動(dòng)研磨也加劇了研磨過(guò)程中的熱化學(xué)作用,使多種熱化學(xué)去除方式所起的作用相應(yīng)增加,這也是超聲振動(dòng)研磨效率提高的原因之一。
- 由圖2可知,在相同條件下,粗粒度(W40)PCD的材料去除率明顯高于細(xì)粒度(W20)PCD的材料去除率,這是因?yàn)榇至6萈CD的表面粗糙度值較大,研磨時(shí)相應(yīng)的摩擦系數(shù)也較大,研磨時(shí)磨粒與PCD表面的金剛石撞擊產(chǎn)生較大的脈沖力;同時(shí)由于細(xì)粒度PCD比粗粒度PCD的結(jié)合更為致密,可較好抑制制造過(guò)程中PCD內(nèi)部產(chǎn)生的微小裂紋和不規(guī)則空穴對(duì)其強(qiáng)度的影響,使金剛石微粒在超聲振動(dòng)研磨中不易發(fā)生脫落和解理性脆斷,因此細(xì)粒度PCD的材料去除率較低。
4 結(jié)論
責(zé)任編輯:商永剛
本文關(guān)鍵詞:振動(dòng)研磨機(jī)
關(guān)于“振動(dòng)研磨機(jī) ”的資訊
- 聚晶金剛石的超聲振動(dòng)研磨機(jī)理研究(2009-07-13)
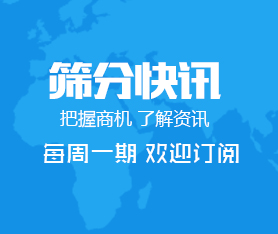
- 資源價(jià)款至少11.8元/方!廣東江門(mén)24...
- 總投資8.3億元!中能建葛洲壩湖南年...
- 朔黃鐵路煤炭年運(yùn)量突破1億噸...
- 浙江交投年產(chǎn)800萬(wàn)噸砂石項(xiàng)目即將正...
- 推動(dòng)集群化發(fā)展!湖南省智慧礦山產(chǎn)...
- 河南省大地水泥取得機(jī)制砂儲(chǔ)存庫(kù)防...
- 湖北荊門(mén)年產(chǎn)600萬(wàn)噸石料生產(chǎn)線順利...
- 疏浚砂綜合利用領(lǐng)域占據(jù)湖北60%以上...
- 包頭鋼鐵集團(tuán)取得一種氧化礦弱磁尾...
- 每年可減少10萬(wàn)余噸建筑垃圾!德州...
- 1《煤礦智能化發(fā)展藍(lán)皮書(shū)》發(fā)...
- 2濟(jì)南:建設(shè)綠色礦山 推進(jìn)生態(tài)...
- 3哈密發(fā)現(xiàn)一處金礦 金品位平均...
- 4山西586處煤礦已實(shí)行采掘紅線...
- 5亞洲最大!赤峰一多金屬礦獲...
- 6中國(guó)多措并舉生態(tài)治理廢棄礦...
- 7廣東累計(jì)完成礦山生態(tài)修復(fù)項(xiàng)...
- 8海南發(fā)布2024年度地質(zhì)成果 鉿...
- 9安徽大力提升戰(zhàn)略性礦產(chǎn)保障...
- 10華為山西智能礦山技術(shù)交流會(huì)...