在粗碎破碎機(jī)中實(shí)施自動(dòng)化系統(tǒng),提高產(chǎn)量40%,消除破碎生產(chǎn)線瓶頸,帶來了更穩(wěn)定的生產(chǎn)和更好的工藝控制。
位于巴西巴拉納州北部的Pedreira Guaravera公司始終注重產(chǎn)品的高質(zhì)量和附加值,以滿足當(dāng)?shù)鼗炷辽a(chǎn)商對(duì)于更多立方體骨料和嚴(yán)格控制產(chǎn)品級(jí)配范圍的要求。這一理念影響到破碎生產(chǎn)線的配置,該公司于近期安裝了中碎圓錐破碎機(jī)和細(xì)碎VSI破碎機(jī)。“雖然我們獲得了滿足客戶要求的產(chǎn)品,但在生產(chǎn)中產(chǎn)生了許多粉料。市場(chǎng)對(duì)這種粉料的需求匱乏,對(duì)我們的經(jīng)營(yíng)造成了麻煩。” Guaravera公司管理合伙人Rodrigo Bastos說。
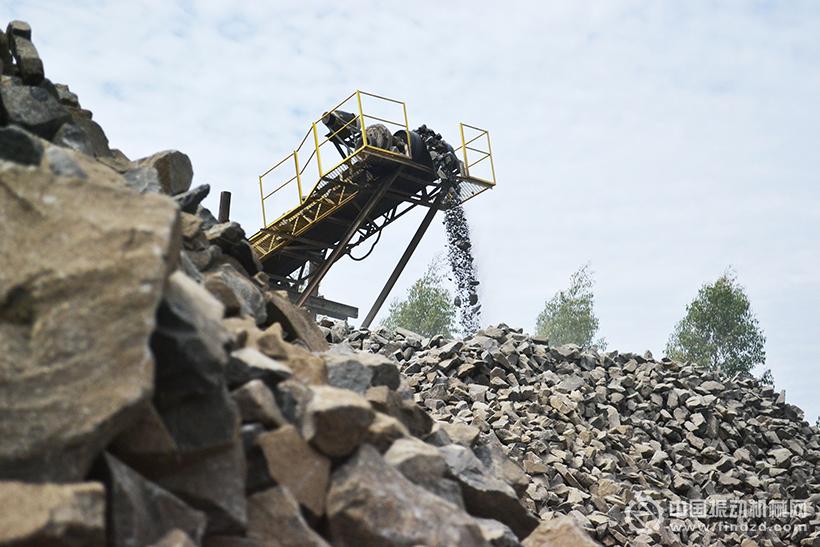
美卓針對(duì)這一問題提出的解決方案是:利用一臺(tái)Nordberg? HP400?破碎機(jī)替代VSI破碎機(jī),將原有的圓錐破碎機(jī)從中碎段移至細(xì)碎段,并更換適用的襯板。“我們還安裝了新振動(dòng)篩,以便更好地分級(jí)物料,從而提高生產(chǎn)率和消除大量粉料產(chǎn)生的負(fù)擔(dān)。然而,粗碎顎式破碎機(jī)的規(guī)格對(duì)于我們的生產(chǎn)規(guī)模而言太小了,它開始成為一個(gè)生產(chǎn)瓶頸。”
據(jù)Bastos稱,目前的市場(chǎng)形勢(shì)不適合投資新的粗碎破碎機(jī)。美卓再次提出了一個(gè)解決方案,即破碎站自動(dòng)化系統(tǒng)。這是一個(gè)極具成本效益的替代解決方案。最初,Bastos反對(duì)這個(gè)想法。因?yàn)樗J(rèn)為對(duì)于目前的員工素質(zhì)來說,采用自動(dòng)化系統(tǒng)是不合適的。但他很快就改變了自己的看法。“在美卓的技術(shù)協(xié)助下,自動(dòng)化系統(tǒng)運(yùn)行快速、順暢,使得粗碎破碎機(jī)的產(chǎn)量提高了40%。”
總體來說,采用了連接到自動(dòng)化系統(tǒng)的多個(gè)傳感器,分別控制破碎機(jī)給料速率、管理卡車向料倉(cāng)的卸料量和監(jiān)測(cè)破碎機(jī)軸承溫度。操作人員通過控制室的顯示器即可監(jiān)控整個(gè)生產(chǎn)工藝。另外,該系統(tǒng)還可生成運(yùn)行和生產(chǎn)報(bào)告。“我們實(shí)施該系統(tǒng)的目的是提高生產(chǎn)率和獲得額外收益。比如,無論操作人員的水平如何,都能確保統(tǒng)一的生產(chǎn)標(biāo)準(zhǔn),還能為我們的決策提供可靠信息。”
運(yùn)營(yíng)收益
產(chǎn)品粒度范圍內(nèi)的生產(chǎn)率和質(zhì)量穩(wěn)定性得到改善,是由于使用了新傳感器控制給料速率,破碎機(jī)可以擠滿給料且無過載。如果由操作人員控制給料,則會(huì)造成處理量波動(dòng),進(jìn)而導(dǎo)致產(chǎn)品質(zhì)量不同。此外,安裝在料倉(cāng)上的傳感器還可控制卡車卸料,改善來自礦山的物料流量。
使用新自動(dòng)化系統(tǒng)后,Guaravera公司在礦山到粗碎破碎機(jī)之間的運(yùn)輸卡車從兩輛增至三輛,以保證破碎機(jī)在最高負(fù)載條件下運(yùn)行。“這樣,我們可以保持一個(gè)恒定的運(yùn)行周期,消除了卡車等待裝載和卸載的非生產(chǎn)時(shí)間。”使用自動(dòng)化系統(tǒng)之前,平均每天50-60趟卡車運(yùn)輸;而現(xiàn)在增加到120趟,保證了連續(xù)生產(chǎn)。
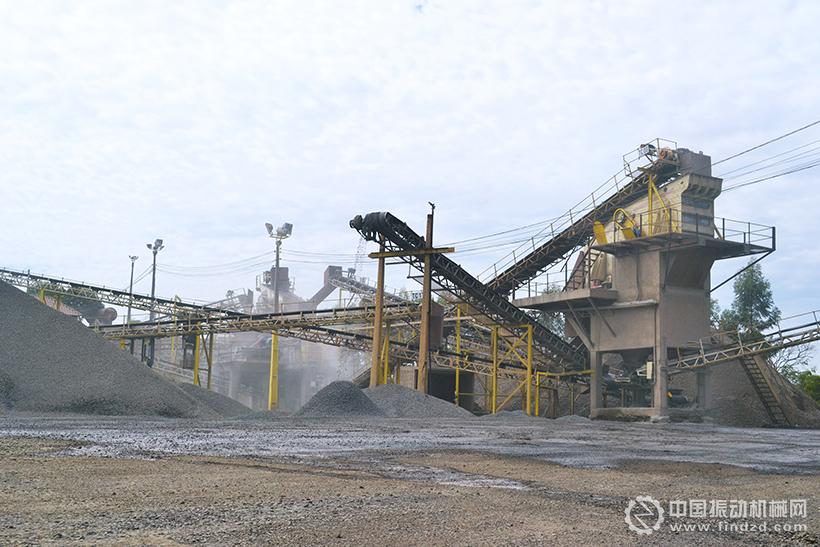
Bastos還強(qiáng)調(diào),該系統(tǒng)為經(jīng)營(yíng)管理提供了一系列重要信息,例如:設(shè)備有效運(yùn)行時(shí)間(無論是負(fù)載或空載),液壓破碎錘的操作次數(shù)和運(yùn)行時(shí)長(zhǎng)。“以前,我們使用手工報(bào)表,現(xiàn)在,可以自動(dòng)生成生產(chǎn)數(shù)據(jù),可靠性更高,有助于我們更快地做出決策。”他舉例說,如果液壓破碎錘頻繁操作,他會(huì)立即干預(yù)采礦作業(yè),以提高爆破質(zhì)量。
該自動(dòng)化系統(tǒng)包括破碎機(jī)軸承溫度傳感器,這有助于維護(hù)保養(yǎng)管理。利用這些傳感器檢測(cè)偏差和預(yù)測(cè)故障。“如果軸承溫度高于規(guī)定值,采石場(chǎng)可實(shí)施計(jì)劃停機(jī),以免導(dǎo)致其他組件故障并采取糾正措施。”美卓高級(jí)自動(dòng)化工程師Fernando Bicalho說。
他解釋說,該系統(tǒng)可存儲(chǔ)一周的操作和運(yùn)行數(shù)據(jù),但目前正準(zhǔn)備將其連接到一個(gè)更強(qiáng)大、更全面的管理平臺(tái)。“在談到工廠自動(dòng)化時(shí),人們會(huì)想到大量的翻新工程或安裝新設(shè)備,然而,我們可以根據(jù)每個(gè)操作需求提供定制的解決方案。”
Bicalhp指出,美卓可以為自有品牌和其他品牌設(shè)備實(shí)施自動(dòng)化系統(tǒng)提供一切技術(shù)支持,從而縮短安裝時(shí)間和減少對(duì)客戶運(yùn)營(yíng)的影響。以Guaravera為例,美卓提供的協(xié)助包括從傳感器和其他裝置的安裝,電氣系統(tǒng)和電機(jī)必要調(diào)整的一切工作。
“在美卓的技術(shù)協(xié)助下,自動(dòng)化系統(tǒng)運(yùn)行快速、順暢,使粗碎破碎機(jī)的產(chǎn)量提高了40%。”